In industrial finishing, abrasive blast booths are crucial equipment that play a significant role in achieving desired surface preparation and cleanliness. Regular maintenance of these booths is not just recommended, but essential for optimal performance and to extend their longevity. The following guide explores how to maintain your abrasive blast booth, focusing on critical aspects such as abrasive recovery, dust collector maintenance, and other tasks that keep your equipment functioning at its best.
The Importance of Regular Maintenance
Abrasive blast booths are integral to many industrial processes, offering consistent results in surface finishing. However, like all heavy machinery, they are subject to wear and tear. Regular maintenance helps to achieve the following:
- Maximize Efficiency: Well-maintained equipment operates at peak efficiency, saving time and resources.
- Extend Equipment Life: Routine checks and timely repairs can significantly extend the lifespan of the machinery.
- Ensure Safety: Regular inspections reduce the risk of accidents and ensure a safe working environment.
- Reduce Costs: Preventative maintenance can prevent costly breakdowns and repairs.
Key Maintenance Areas
1. Abrasive Recovery Systems: Abrasive recovery is central to efficiently operating blast booths. To handle the recyclable media properly, recovery systems must be free of obstructions and functioning correctly. Cleaning and inspecting the recovery system should be part of a regular maintenance schedule.
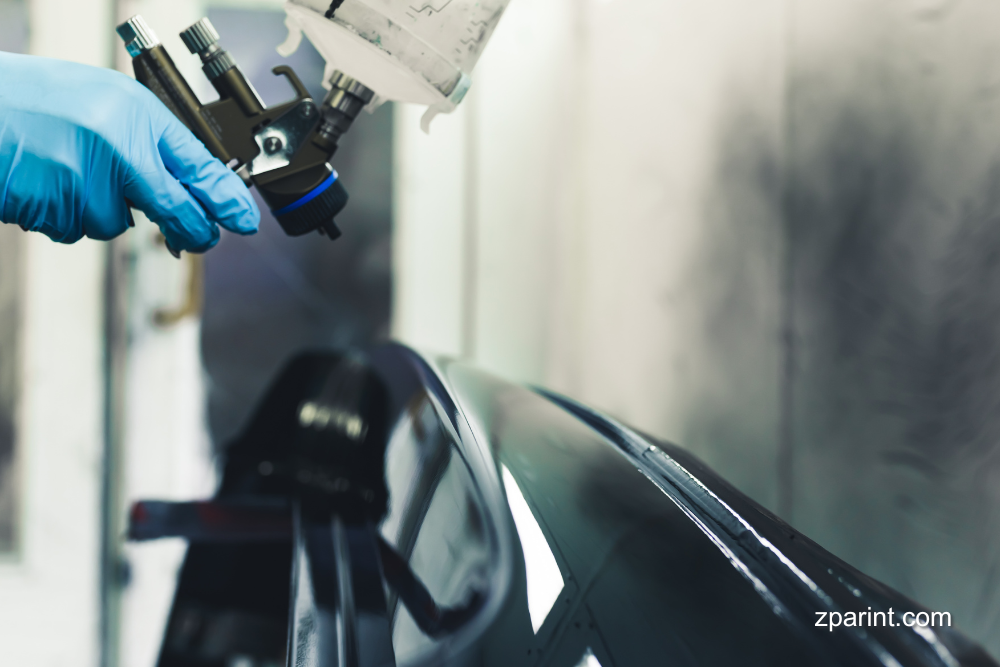
2. Dust Collector Maintenance: Dust collectors prevent the accumulation of fine dust particles, which can pose a health hazard and compromise visibility. Regularly check filters and replace them as necessary to ensure that the dust collection system remains effective. Ensure that the bags and cartridges in dust collectors are intact and functioning.
3. Nozzle Wear: Due to the high-speed abrasive blast media, nozzles are subject to significant wear and tear. Inspect nozzles frequently for any signs of wear or damage. Worn nozzles can reduce efficiency and precision, ultimately affecting the quality of the finished product.
4. Protective Lining: The protective lining inside an abrasive blast booth shields the booth from wear and tear caused by the abrasive materials. Inspect the lining regularly for signs of damage and replace it when necessary to prevent further damage to the booth structure.
5. Visibility and Lighting: Adequate visibility ensures precise work and prevents accidents. Clean and maintain the lighting fixtures regularly to ensure they are operating efficiently. Replace any burned-out bulbs or faulty fixtures promptly.
Creating a Maintenance Schedule
To keep your abrasive blast booth in optimal condition, develop a maintenance schedule that covers daily, weekly, and monthly inspections:
- Daily Checks: Inspect the nozzles and hoses for wear, ensure all safety equipment is in place, and verify that the dust collector is operating correctly.
- Weekly Checks: Clean the dust collector filters and verify the function of the abrasive recovery system. Ensure all lighting and protective measures are in place.
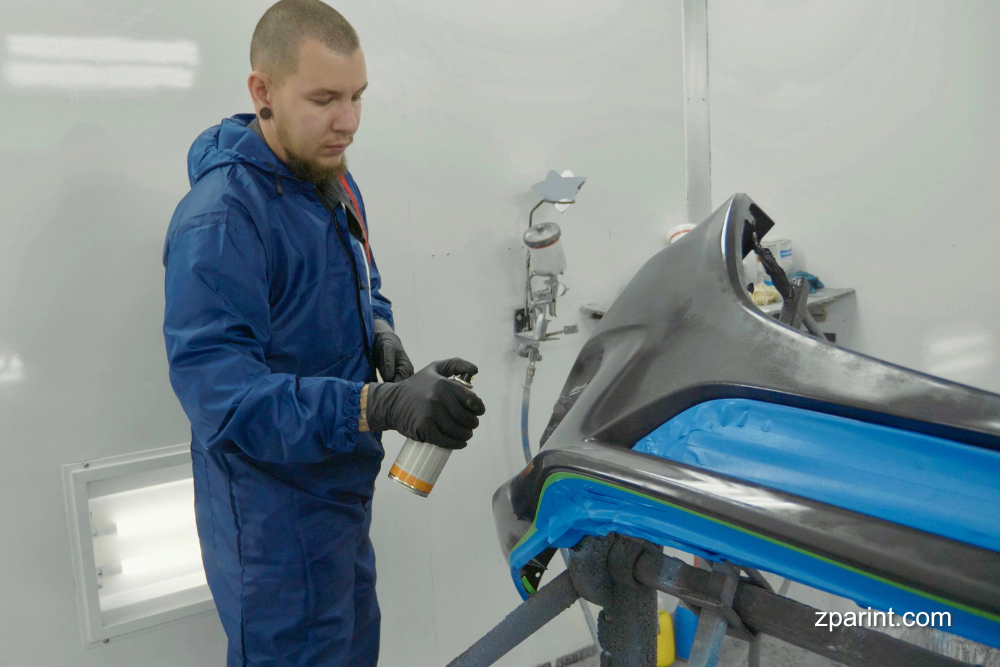
- Monthly Checks: Thoroughly inspect the protective lining, check the overall condition of all mechanical components, and test to ensure the entire system functions correctly.
Partner with ZPar International for Custom Solutions
Maintaining your abrasive blast booth is a continuous process that warrants attention and care. Partnering with industry leaders like ZPar International can make all the difference for customized industrial finishing systems. With a reputation for excellence, ZPar International provides tailored solutions designed to meet your unique requirements, offering enhanced operational reliability and efficiency.
Incorporating proactive maintenance practices into your routine ensures that your abrasive blast equipment remains in peak condition, enhances safety standards, and reduces maintenance costs. By following these guidelines and utilizing expert resources, such as ZPar International, your abrasive blast booth will continue to deliver high-quality results for years to come.
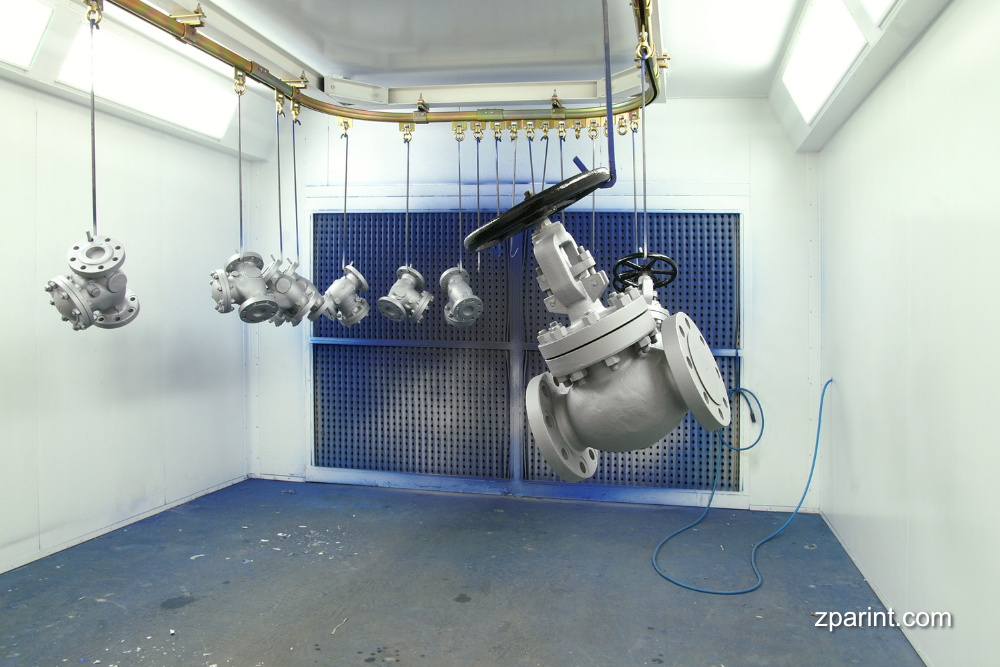